
Jetzt teilen:
Durch einen strategischen Ansatz für die digitale Transformation unter Verwendung eines digitalen Fadens können Hersteller die Produktentwicklung beschleunigen, die Beschaffungs- und Produktionskosten senken und Erkenntnisse gewinnen, um Engpässe in der Lieferkette zu umgehen.
Wenn Sie 10 Führungskräfte aus der Fertigungsindustrie nach der Definition von „digitaler Transformation“ fragen, werden Sie wahrscheinlich 10 verschiedene Antworten erhalten. Glücklicherweise ist eine strenge Definition für die digitale Transformation oder Industrie 4.0 nicht so wichtig wie die Art und Weise, wie Hersteller ihre Strategien umsetzen, um ihre Geschäftsziele zu erreichen und ihre Erfolge zu messen. Hersteller, die die digitale Transformation (Digitalisierung) effektiv umsetzen, können ihre Produktivität und Gewinne steigern, die Markteinführung beschleunigen und die Widerstandsfähigkeit der Lieferkette stärken.
Im Kern bietet die digitale Transformation eine Technologie- und Datengrundlage, die interoperabel und skalierbar ist und über die nötige Flexibilität verfügt, um heutige und künftige Geschäftsanforderungen zu erfüllen. Und wie jeder neue Ansatz erfordert auch dieser die richtige Führung, die richtigen Mitarbeiter, Prozesse und die Akzeptanz der Mitarbeiter, um erfolgreich zu sein.
Die digitale Transformation ist nicht monolithisch: Sie umfasst mehrere Funktionen, die nahtlos zusammenarbeiten müssen, um den Geschäftswert zu steigern. Wenn eine Funktion der digitalen Transformation nicht effizient arbeitet oder nicht auf die anderen abgestimmt ist, wird der gesamte Geschäftsprozess blockiert. Tabellenkalkulationen und benutzerdefinierte Systeme enthalten beispielsweise isolierte Daten, die nicht automatisch in Geschäftssysteme integriert werden können – und die auch nicht Teil eines digitalen Prozesses sind.
Die 4 Säulen der digitalen Transformation für die Fertigung
Aus unserer Sicht besteht die digitale Transformation in der Fertigung aus vier zentralen technologischen Säulen. Wenn Sie den Wert, die Rolle und die Möglichkeiten jeder einzelnen Säule verstehen, können Sie die neuen Funktionen auf die vorrangigen Geschäftsanforderungen abstimmen:
- Interoperable Daten und Technologien ermöglichen eine unternehmensweite Zusammenarbeit. Durch die Verwendung einer einzigen Datenquelle während des gesamten Produktlebenszyklus erhalten Unternehmen Einblicke, um schnell und sicher fundierte Entscheidungen zu treffen. (Manche mögen dies auch als eine enge Sichtweise der digitalen Transformation betrachten).
- Der digitale Zwilling umfasst digitale Konstruktionsdateien (3D-CAD) und zugehörige Produkt- und Fertigungsinformationen (PMI). Er ist das digitale geistige Eigentum (IP) eines Unternehmens und sollte als Grundlage für die Beschaffung und Fertigung dienen, um die Abläufe zu beschleunigen und Risiken zu verringern.
- Der digitale Faden verknüpft die digitale und die physische Welt der Hersteller. Er verbindet den digitalen Zwilling und Produktinformationen, einschließlich Beschaffungs-, Fertigungs- und Außendienstdaten. Und er kann Geschäftsprozesse über traditionell getrennte Abläufe hinweg erweitern (z. B. Produktdesign und Beschaffung).
- Digitale Fabriken ermöglichen die Simulation und Analyse von Design for eXcellence (DfX) in den Bereichen Planung, Design, Beschaffung und Fertigung. Teams verwenden präzise digitale Zwillingsspezifikationen, um Kosten und Produktionsszenarien zu berechnen, um ausgelagerte Produktionsoptionen weltweit zu vergleichen, interne Fertigungskapazitäten zu bestimmen und verschiedene Fertigungsprozesse zu bewerten. Der Zugang zu aktuellen, realen Preisen und der Verfügbarkeit in der Lieferkette ist für eine effektive Planung entscheidend.
Die vier Säulen der digitalen Fertigung sind: Daten und Technologien, der digitale Zwilling, der digitale Faden und die digitale Fabrik
Wie der digitale Faden das gesamte Produktentwicklungsteam verbindet -
The four pillars of digital manufacturing are: data and technologies, the digital twin, the digital thread, and the digital factory
Wie der digitale Faden das gesamte Produktentwicklungsteam verbindet
Der Wert der digitalen Transformation wird größtenteils durch den digitalen Faden bestimmt: wie Unternehmen Abteilungen und Abläufe miteinander verbinden und Informationen nutzen, um schnell Entscheidungen zu treffen. Hersteller, die einen digitalen Faden durch den gesamten Produktentwicklungszyklus weben, können den digitalen Zwilling mit Daten aus der physischen Welt verbinden – einschließlich Fertigungskapazitäten, Beschaffungs- und Kosteninformationen aus der Lieferkette, Außendienstberichten und anderen Vorgängen.
Der geschlossene Prozess des digitalen Fadens bietet eine einzige, zuverlässige Informationsquelle, auf die die Beteiligten zurückgreifen können, um fundierte Entscheidungen zu treffen. So können die Teams schneller und effizienter arbeiten, indem sie aktuelle digitale Produktinformationen nutzen.
So können beispielsweise Kostenentwicklungsteams frühe Entwürfe überprüfen und Aktualisierungsempfehlungen abgeben, um die Herstellbarkeit und andere Probleme zu lösen. Und sobald Ingenieure ein CAD-Modell aktualisieren, kann die Beschaffung die überarbeiteten Spezifikationen sofort nutzen, um aktualisierte Angebote einzuholen.
Und Daten aus der Praxis können in Konstruktionsaktualisierungen einfließen, z. B. wenn ein Serviceteam ein Leistungsproblem feststellt, wenn das Produkt in einer Umgebung mit hohen Temperaturen eingesetzt wird. Oder Nutzungsdaten von vernetzten Produkten, die weltweit eingesetzt werden, können aufzeigen, dass ein aktueller Produktmotor nicht ausreichend ausgelastet ist und durch eine weniger leistungsstarke, kostengünstigere Alternative ersetzt werden kann, ohne dass die Leistung beeinträchtigt wird.
5 Schlüssel für einen starken digitalen Faden in der Fertigung
Der digitale Faden kann Mehrwert schaffen, indem er Automatisierung ermöglicht, Geschäftsprozesse zwischen Abteilungen erweitert und aktuelle Geschäftsdaten für fundierte Entscheidungen bereitstellt. Im Folgenden finden Sie fünf Schlüssel, die Hersteller bei der Einführung eines effektiven digitalen Konzepts berücksichtigen sollten.
1. Verbinden Sie Stakeholder, um Produktivität und Gewinne zu steigern
Richten Sie eine „Single Source of Truth“ ein, die auf kritische Systeme zurückgreift und dann den digitalen Faden nutzt, um Leistungs- und Fertigungsdaten zwischen dem digitalen Zwilling und nachgelagerten Anwendungen (z. B. Konstruktion, Beschaffung, Fertigungspartner usw.) zu verbinden. Durch die Beseitigung von Abteilungssilos können Produktteams gleichzeitig entwerfen und validieren und mit ihren Kollegen aus der Kostenplanung und der Beschaffung zusammenarbeiten, um sicherzustellen, dass die Produkte herstellbar sind und die Zielkosten sowie die Produktionsfristen eingehalten werden.
2. Vereinfachung und Beschleunigung der Abläufe durch Automatisierung
Die Automatisierung spielt eine wichtige Rolle bei der Steigerung der Effizienz und der Reduzierung der betrieblichen Komplexität. Integrieren Sie die Automatisierung in das Design for Manufacturability (DFM) und die Fertigungskostenanalyse. Nutzen Sie Regeln, Rollen und Auslöser, um Gruppen/Teams zu alarmieren, um Maßnahmen zu ergreifen, Berichte für leitende Mitarbeiter zu erstellen und vieles mehr. Beispiele aus der Fertigung können sein:
Identifizierung von Komponenten für ein Re-Design oder ein neues Angebot mit hohen Kostenauswirkungen
Identifizierung von Ausreißern mit Problemen bei der Herstellbarkeit
Benachrichtigung der Beteiligten über bestimmte risikoreiche Teilekonstruktionen zur sofortigen Überprüfung
Sehen Sie sich dieses kurze Video an, um zu erfahren, wie der digitale Faden das Produktdesign näher an die Produktion heranführt.
3. Verbessern Sie die Planung mit faktenbasierten Einblicken
Eine effektive strategische Planung erfordert die Fähigkeit, auf Informationen wie robuste Produktdaten, detaillierte Fertigungskostenmodelle und regionale Lieferantenbibliotheken zurückgreifen zu können. Führungskräfte können diese Daten für Planungs- und Analyseszenarien nutzen, wie z. B.:
Bewertung der Realisierbarkeit der Verwendung eines Ersatzmaterials zur Umgehung von Verzögerungen in der Lieferkette
Untersuchen Sie, wie sich verschiedene Fertigungsprozesse auf die Produktionskosten und die Verfügbarkeit auswirken
Durchführung einer Matrixkalkulation zum Vergleich regionaler Fertigungskostenunterschiede nach Arbeit, Material, Gemeinkosten, Ausrüstungs-/Anlagensätzen und Gewinnspanne
Erwägen Sie andere Was-wäre-wenn-Szenarien, um für mögliche Marktveränderungen zu planen.
4. Nutzung der digitalen Fabriksimulation zur Optimierung der Fertigung
Dynamische Schwankungen der Materialpreise, regionale Fertigungskosten und Hindernisse in der Lieferkette machen den Zugang zu aktuellen Informationen unerlässlich. Da ERP-Systeme historische Preisinformationen enthalten, bieten sie nur einen richtungsweisenden Einblick. Aktuelle Material- und Fertigungspreise geben den Beschaffungsteams leistungsstarke Werkzeuge an die Hand, um Kosteneinsparungen zu ermitteln und Produktionsziele zu erreichen. Eine optimale digitale Darstellung einer physischen Fabrik umfasst:
Regionale Datenbibliotheken: Eine umfangreiche Datensammlung zur Berechnung der Herstellungskosten und zur Durchführung von Szenarien für die Produktion in verschiedenen Regionen.
Fertigungskostenmodelle: Recherchieren Sie kostensparende Produktionsalternativen durch Kostenmodellsimulationen in Minutenschnelle.
Erfahren Sie mehr über Digitale Fabriken in unserem umfassenden Leitfaden hier.
5. Verbessern Sie die Agilität der Lieferkette (und reduzieren Sie das Risiko)
Reduzieren Sie den Zeit- und Kostenaufwand für die Erstellung von Angeboten und Ausschreibungen. Hersteller können die Beschaffung über eine Collaboration Engine beschleunigen, um die detaillierten Fertigungskosten und -fähigkeiten der Lieferanten zu verstehen. Digitale Fabriken können auch zur Rationalisierung des Angebotsprozesses selbst beitragen. Bei etablierten Hersteller-Lieferanten-Beziehungen kann das Beschaffungsmodell so verfeinert werden, dass ein „Zero-RFQ“-Prozess unterstützt wird, bei dem die Hersteller eine Bestellung für ein Design aufgeben, ohne überhaupt auf ein Angebot zu warten. Lesen Sie, wie der Schienenverkehrshersteller Alstom seinen Beschaffungsprozess durch die Einführung eines Zero-RFQ-Prozesses drastisch verbessert hat.
Entwickeln Sie einen starken digitalen Faden für messbaren Erfolg
Laut einer Umfrage des Branchenanalysten Gartner aus dem Jahr 2021 planen mehr als 80 % der CEOs, ihre Investitionen in die digitale Transformation zu erhöhen. Dies spiegelt zwar die Dringlichkeit wider, neue Fähigkeiten zu erlangen und die Kosten zu senken, doch es ist unklar, wie erfolgreich diese Bemühungen sein werden. The Keenfolks, ein Beratungsunternehmen, berichtet, dass fast drei Viertel der Unternehmen Schwierigkeiten haben, den ROI ihrer Ausgaben für die digitale Transformation zu berechnen.
Hersteller haben eine klare Chance, Kosten und Markteinführungszeiten zu senken, indem sie das Produktdesign eng mit der Beschaffung und Produktion abstimmen. Initiativen zur digitalen Transformation, die den digitalen Faden nutzen, um Abteilungen zu verbinden, haben die Chance, schnell quantifizierbare Vorteile zu erzielen. Unternehmen können den Erfolg messen, indem sie die neuen digitalen Transformationsfunktionen bewerten, die durch den digitalen Faden aktiviert wurden, und wie umfassend sie im gesamten Unternehmen genutzt werden.
Möchten Sie den digitalen Faden nutzen, um Ihr Unternehmen voranzubringen?
Registrieren Sie sich für unsere 10. jährliche Manufacturing Insights Conference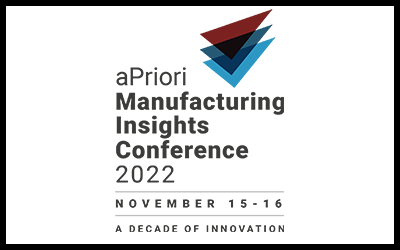